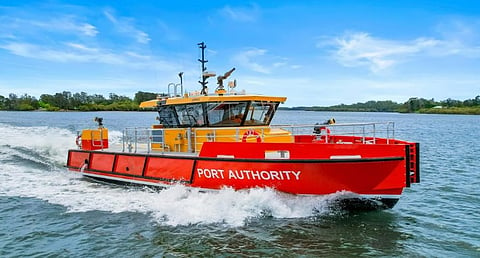
The Port Authority of New South Wales in Australia recently took delivery of two new firefighting vessels built by local company Birdon.
Burra and Girawaa are among the fastest response vessels ever commissioned by the Port Authority. The aluminium monohull vessels are designed to respond to major on-water incidents, including firefighting operations both on and from the water. Such a capability is necessary, as each year, Port Authority NSW responds to over 1,000 incidents in Sydney ports alone, with vessel fires, oil pollution incidents, and water mishaps requiring rescue being among the most common.
The vessels each have an LOA of 17.8 metres (58.4 feet), a beam of 5.5 metres (18 feet), and a draught of only 0.8 metres (2.6 feet). The propulsion arrangement on each vessel consists of two Scania DI16-076M engines that each produce 662 kW (888 hp) at 2,050 rpm each driving Namjet TJ611 waterjets via ZF 665 gearboxes. Electrical power is supplied via alternators while two Yanmar auxiliary engines are also available for driving the firefighting pumps.
Despite the engine room on each vessel having two main and two auxiliary engines, ample space is available for easy access during operations, servicing, and maintenance.
"The customer put out a fairly broad brief that was not too specific, providing a great opportunity to tailor and develop something quite unique for them," Chris Brown, Project Manager at Birdon, told Baird Maritime. "They didn't even specify if it needed to be a monohull or catamaran hull type, so they left it quite open. The main feature was to have a firefighting vessel, but they wanted to also accommodate various other capabilities appropriate for the Sydney Harbour area."
Brown said that the owner wanted other key features including a crane and an open aft deck to accommodate a range of operations, though firefighting would remain the vessels' primary role.
"The customer had a fairly urgent need. They were looking to replace vessels that were built in the mid-1980s and they were built more on a platform more similar to a tug. They were coming to the end of their life cycle and the Port Authority was replacements that would be more suitable to their requirements."
The result was a purpose-built vessel design tailored to unique operations in Sydney and Botany Bay. In fulfilment of port authority requirements, the vessels were NCV survey-compliant and were capable of top speeds in excess of 20 knots, in addition to boasting excellent visibility and improved man overboard recovery capability.
The key feature of the vessel is the firefighting system, which includes firefighting monitors that can be pointed in all directions fed by two fire pumps capable of discharging 16,000 litres (4,200 gallons) of sea water per minute over a distance of 85 metres (280 feet). Additionally, there is a monitoring system that measures the volume of water discharged by the firefighting system. These capabilities enable the vessels to support the activities of the port authority's partner agencies such as Maritime NSW and the NSW Police.
"We worked closely with the owners to design a layout that was tailored to their specific needs, including the placement of controls, navigation elements, and communication systems," added Brown. "However, one of the biggest challenges was the incorporation of the firefighting system, particularly the placement of the monitors. We've placed one on the bow in front of the wheelhouse, one on the wheelhouse roof, and two on each aft corner of the vessel.
"These monitors needed to be piped through the vessel, from a central location where they pumps are driven. We had a relatively small platform to work with, but we built a lot of capability into this space. This is true not just for the firefighting system, but also for a lot of other things that the firefighting system requires."
Birdon, along with one of its subcontractors, also developed an innovative human interface system where all the valves and functionality of the system can be controlled from a single pilot seat up in the wheelhouse.
This dedicated firefighting operation station features a touchscreen for activating the individual monitors, open and close the various valves on the system, and change their settings from a straight stream to a fog setting/cone-shaped pattern.
This operation station also features a joystick and various controls for the pump engines. This integration – together with a wheelhouse that has a 360-degree view with large glass windows and skylight-type glass on the the forward windows so that the crew can look upwards – means the operator does not have to move from the comfort of one seat within the wheelhouse to control the entire firefighting system including seeing where the monitors are spraying at all times.
Should the master decide to get closer to the action, a secondary helm station is also fitted outside the wheelhouse.
"Another feature that complements the firefighting system, which posed a challenge that was ultimately resolved successfully, is our station-keeping capability," Brown told Baird Maritime. "We chose to partner with Vector Controls on the system, which uses GPS input and a specialised programmed motion control system that can maintain the vessel's location as well as heading at the same time using the propulsion system and the bow thruster. So, by simply flicking a switch, the control system will take over and maintain its location without human input."
Brown added that while the new response vessels are not equipped with the extensive redundancy found in the oil and gas industry, the station-keeping system is robust, maintaining location and heading to overcome various environmental effects such as currents or wind. The master is always on station, but the vessel can control its location and heading simultaneously. The capability is crucial during firefighting, allowing each boat to remain in a specific location despite smoke and other factors.
"The force of the water discharged from the firefighting monitors is powerful enough to propel the vessel in any direction, depending on how the monitors are aimed. The station-keeping system counteracts this force, ensuring the vessel remains in position. While the station-keeping system isn't actively integrated to the firefighting system, it detects that the vessel is being forced in a direction allowing both system to work together effectively during firefighting operations."
Brown said that, as the first of its class, the vessel faced a number of challenges during construction. The design was refined throughout the construction process. There were also difficulties in procuring and integrating components, particularly the station-keeping system from Vector Controls, as the company is based in the United States and there is a significant time difference.
Brown explained that the installation of the station-keeping system also involved trial and error due to the level of programming and customisation during the commissioning period. The vessels also needed to be moved from side to side ("crabwalk") and moved evenly and predictably.
"Part of the challenge lay in the integration of the station-keeping system with the engines, drives, bow thruster, and GPS, all of which were separate OEM components procured from different parts of the world. Despite these obstacles, the vessels were successfully completed. Though not be extremely large, a great deal of functionality has been built into this compact platform."
A key consideration was designing the layout of the associated piping to enable seamless operation of the roof-mounted firefighting monitor while ensuring uninterrupted activity in the wheelhouse.
"We had to do a lot of tests for the piping system. Every section of pipe needed to be processed and pressure tested. We put together a report for each section where we had done the pressure testing, and it came up very nicely in the end."
The vessels also needed to generate only minimal noise even with the engines running the fire pumps. Brown said that, on a platform only 17.8 metres long, noise control became imperative.
"There was significant isolation required in the system," said Brown, "and we had gain a deeper understanding about the pumps and their installation. It wasn't just about insulation to prevent airborne noise, but also about isolation of structure-borne noise. We successfully reduced get the noise to below the safety requirements. Despite the pumps being directly beneath the wheelhouse, the crew don't need hearing protection."
Brown explained that, due to the customer's unfamiliarity with jet drives, Birdon provided initial crew training.
"Their crew were used to the vessels they had in their fleet, which are all propeller-driven. However, jet drives provide functionality, which is difficult to achieve with propellers such as crabwalking directly port or starboard. So, we focused on ensuring the customer was happy.
The new boats will be deployed one each to Sydney and Botany Bay, where they will also serve a general patrol function in addition to firefighting, pollution response, and water rescue.
"The owner's existing vessels are no longer suitable for operations," Brown told Baird Maritime. "They were larger, less efficient, and not very fast. This made them less than ideal for responding to emergencies. The new vessels are better suited to the current operational profile and requirements, with a low draught that allows them to get close to shore and fight fires more effectively."
"The customer also specified that the mast must fit beneath one of the bridges further up the river in Sydney. To accommodate this requirement, the mast is designed to be released and lowered to get underneath, allowing passage beneath bridges."
There is also an anchor winch controlled from a pendant on the foredeck, as well as quick couplings for hydraulic points. This allows the crew to couple up the booming reel module onto the aft deck and use it in the harbour.
A hydraulic boom crane will be used for loading and offloading cargo, a deck-mounted hydrant will be used for coupling a fire hose, and a fixed induction draw point on the deck for inducting foam compounds into the firefighting system. The percentage of foam inducted can be customised anywhere as required.
"We have an aft platform for rescue operations, which is at the waterline for picking up people," said Brown. "There's a ladder that can be integrated into the platform, which can be quickly deployed to the aft platform via mounting points. There are storage locations for equipment packs, and large engine hatches for easy access to the engine room."
Lashing points are fitted around the vessel for harnessing during rescue operations. There are also ball cleats around the vessel with pelican hooks for open access over the side and harness points for individuals to harness themselves when working in open areas.
The vessels also each have lightbars and a push-knee arrangement on the bow with vertical fenders for pushing things around and docking.
"The customer did regular visits to Birdon's shipyard in Port Macquarie at least once a month, and they were actively involved in discussing and deciding many of the solutions," added Brown.
Burra & Girawaa | |
SPECIFICATIONS | |
Type of vessel: | Firefighting and rescue vessels |
Classification: | NSCV C2 |
Port of registry: | Sydney, Australia |
Flag: | Australia |
Owner: | Port Authority of New South Wales, Australia |
Operator: | Port Authority of New South Wales, Australia |
Designer: | Birdon Group, Australia |
CAD software: | Solidworks |
Builder: | Birdon Group, Australia |
Hull construction material: | Aluminium |
Superstructure construction material: | Aluminium |
Deck construction material: | Aluminium |
Plate cutting: | Bluescope |
Length overall: | 17.8 metres (58.4 feet) |
Length waterline: | 17.5 metres (57.4 feet) |
Length bp: | 17.8 metres (58.4 feet) |
Beam: | 5.5 metres (18 feet) |
Draught: | 0.8 metre (2.6 feet) |
Depth: | 2.4 metres (7.9 feet) |
Main engines: | 2 x Scania DI16-076M, each 662 kW (888 hp) at 2,050 rpm |
Gearboxes: | 2 x ZF 665 |
Propulsion: | 2 x NAMJet TJ611 Waterjets |
Auxiliary engines: | 2 x Yanmar 6LY2M-WST, each 294 kW (394 hp) |
Side thrusters: | CT 550 |
Steering system: | Vector Controls |
Maximum speed: | 27 knots |
Cruising speed: | 18 knots |
Hydraulic equipment: | Vivolo; Danfoss |
Electronics supplied by: | Ultimate Marine Power |
Displays: | 2 x Simrad NSS evo3S |
Radar: | Simrad Halo24 |
Depth sounder: | Simrad XSONIC SS60 SS |
Dynamic positioning: | Vector Controls |
Radios: | 2 x ICOM 330 VHF |
Compass: | Silva 100BC |
GPS: | Simrad HS60 |
AIS: | Simrad V5035 Class A |
Audio system: | Fusion MS-RA60 Marine Stereo |
Monitoring system: | ITIM |
Cameras: | Hikvision CCTV |
Winch: | Muir Storm VRC3500 |
Crane: | Fassi M40AFM.1.12 |
Anchor: | SHHP |
Fendering: | D-type |
Paints: | International |
Seating: | Recaro |
External lighting: | Hella |
Deck surface finish: | Non-slip aggregate |
Interior designer: | Birdon Group |
Interior fitout: | Birdon Group |
Safety equipment: | Lifejackets |
Firefighting equipment: | 2 x Darley pumps; 4 x Elkhart Brass monitors; Ultimate Marine Power HMI control |
Type of fuel: | Diesel |
Fuel capacity: | 4,400 litres (1,200 gallons) |
Freshwater capacity: | 120 litres (32 gallons) |
Sewage capacity: | 120 litres (32 gallons) |
Accommodation: | Galley; toilet |
Crew: | 6 |
Operational area: | Sydney, Australia; Botany Bay; Australia |