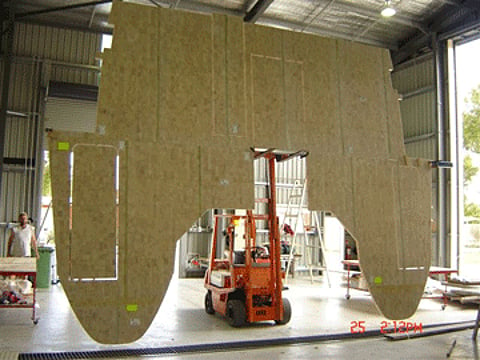
Composite construction has again been proven as a viable alternative to aluminium for the construction of commercial vessels with the successful sea trials, and initial commercial operation, of the 24-metre long whale watching catamaran ferry, 'Spirit of Hervey Bay', in Queensland, Australia.
The vessel has been build using ATL Composites' DuFLEX Composite Panel System. These component packs, which are created at ATL's facility on Australia's Gold Coast using state-of-the-art CNC routing machinery, are well recognised throughout the boatbuilding industry for their cost-efficiency especially through a reduction in labour costs and the minimisation of waste material.
"What has been most encouraging is that 'Spirit of Hervey Bay' clearly shows there is no limit when it comes to the size of the Component Packs that ATL can produce," said designer Noah Thompson. "Bigger projects are now on my drawing board using DuraKore and DuFLEX routed packages."
Another benefit derived from DuFLEX structural panels is that the design requires fewer frames and ring frames to form the structure of the vessel when compared to a similar sized aluminium vessel. This reduction in frames and the light weight properties of the DuFLEX Panels contributes to a significant weight saving overall.
This weight saving extends further because in being lighter the vessel requires smaller engines and less fuel capacity to achieve design performance targets. The design specification for 'Spirit of Hervey Bay' required a service speed of between 18 and 20 knots with 245 passengers on board.
Currently she is achieving 21 knots at 1,800rpm, and there is ample evidence of a saving in fuel costs compared to other similar sized boats. The vessel is performing equally well at light-ship as it does at full displacement, with only a slight change in speed or rpm.
'Spirit of Hervey Bay' took only 15 months to build. It was engineered by ATL Composites to meet Australian Standard USL 1C/1D. The hulls were strip planked in DuraKore over male frames while the remainder of the vessel was manufactured and supplied by ATL as a DuFLEX Component Pack, including hull topsides, tunnel, transom, bulkheads, soles, decks and superstructure.
ATL Composites also manufactured and supplied lightweight non-structural panels for the ceilings and the fibreglass reinforcements used throughout. Their high performance KINETIX Professional Epoxies were used for additional laminating applications.
DuFLEX composite panels are available with cores of end-grain balsa, structural linear foam, cross-linked foam, or aramid honeycomb. These are all laminated using a high performance epoxy resin that is reinforced with multiaxial E-fibreglass or carbon fibre. The type and thickness of the core, fibre orientation and ply schedules are based on design or engineering specifications that are established around weight targets, stress and impact loads, and other design parameters.
To reduce wastage, ATL Component Packs have all parts required for the project nested together within the panels. These panels are sequentially numbered to indicate the correct joining sequence, and a nesting diagram detailing each part number and a description of it, is supplied for easy identification.
For further information contact: