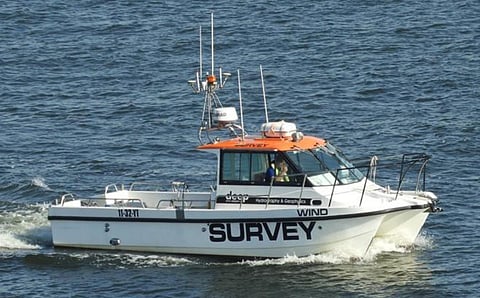
US-based unmanned technology company Sea Machines Robotics recently held a webinar in conjunction with Netherlands-based survey specialists Deep and Simon Remote Survey to discuss the merits of using remote navigation systems in conducting surveys close to the coast.
Jurgen Beerens, Deep's Chief Commercial Officer, and Marteyn Blok, CEO of Simon, related that remote navigation technology offered a host of benefits in nearshore survey operations. Safety was highlighted since the technology would allow fewer people to be put at risk out at sea. It also meant a reduced carbon footprint, since eliminating the act of transporting crews to and from vessels at work sites also eliminated the companies' reliance on vehicles and other means of support.
Just as importantly, the technology would enable more precise and efficient survey operations, thus allowing sister companies Deep and Simon to "do more with less." Specifically, the idea is to have only one platform be capable of performing different types of survey missions utilising different equipment and sensors and covering different parameters on one trip, a concept of "ad hoc surveys" as stated by Blok.
A survey boat operated by Deep was fitted with an autonomous command and remote helm control system developed by Sea Machines. This allowed the vessel to be operated remotely from a shore control station – Deep's office in Amsterdam, in this case – thereby eliminating the need for an onboard crew to manoeuvre it on the water. Further, the system has been customised to allow the shore-based operator to also have full control of the vessel's array of onboard equipment such as cameras, sonars, hydrophones, winches, cranes, and davits.
To further streamline operations, the decision was made to equip the vessel in such a way that ad hoc surveys can be performed. There will be no more need to carry out pierside pre-configuration, which includes installing and removing sensors, before every voyage since the vessel can already be deployed with all the equipment it would need for a range of specific survey types. The system is also designed to allow the shore-based operator to remotely instruct the boat to immediately perform type-specific surveys depending on the equipment installed on board.
One other notable feature of the Sea Machines system is its ability to collect and transmit the survey data that were gathered through the different sensors installed on the Deep boat. The transfer of data is done in real-time via 4G or satellite connection depending on the distance between the survey boat and the shore control station (4G if less than five nautical miles).
The collected data are then stored in a web-based project portal that Deep and Simon technicians can access at any time for future reference, such as in performing follow-up projects in areas that were surveyed before. The use of electronic data contributes to further reduction in the two companies' respective carbon footprints, since there would be no need for printing survey-related data on paper and storing all of it in a physical location.
The Sea Machines system applies the concept of sensor fusion to provide operators with a detailed view of various data gathered from onboard sensors. In the case of Deep, the vessel's location, the weather, project condition i.e. whether complete or incomplete, and other items requiring attention are readily available for the shore-based operator to view and access without having to switch between physical consoles.
The system also features alert-based messaging. When any factor is outside the pre-determined parameters for safe survey work i.e. weather, an onboard fire, engine trouble, etc., the shore-based operator is immediately alerted and "all stop" may be initiated on all onboard interfaces to prevent the survey boat from sailing while "blind," which could result in damage or injury.
The goal of Deep and Simon is to eventually be able to transition from minimally manned survey missions to fully unmanned missions with the help of Sea Machines' autonomous command and remote helm control system. The two companies believe this can be achieved as the results from recent trials have proven the viability of remote operations in its nearshore surveys in the Wadden Sea.
Because the Sea Machines system is designed to be easily integrated into existing vessels as well as newbuilds, both Deep and Simon are confident that additional vessels can be equipped appropriately in less time and at minimal cost, thereby allowing unmanned nearshore surveys to be conducted on a much wider scale.